Schlechte Wasserbeständigkeit, unebene Oberfläche, hoher Pulveranteil und ungleichmäßige Länge? Häufige Probleme und Verbesserungsmaßnahmen bei der Aquaristik-Futterproduktion
Bei unserer täglichen Produktion von Aquakulturfutter sind wir in verschiedenen Bereichen auf Probleme gestoßen. Hier sind einige Beispiele, die wir gerne mit Ihnen besprechen möchten:
1. Formel
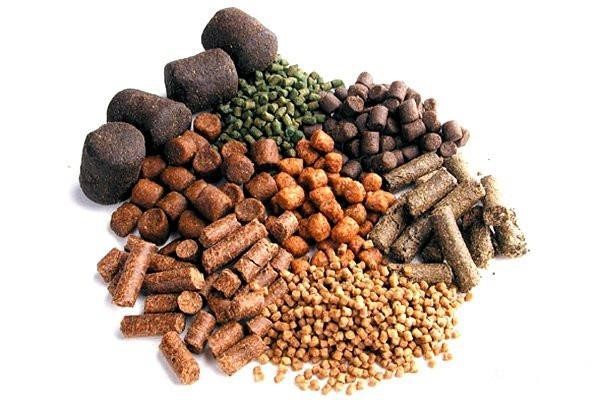
1. In der Rezeptur von Fischfutter gibt es verschiedene Arten von Mehlrohstoffen, wie Rapsmehl, Baumwollmehl usw., die zu den Rohfasern gehören. Einige Ölfabriken verfügen über fortschrittliche Technologie, und das Öl wird grundsätzlich mit sehr geringem Gehalt trocken frittiert. Darüber hinaus sind diese Rohstoffe bei der Produktion schwer saugfähig, was sich stark auf die Granulierung auswirkt. Darüber hinaus ist Baumwollmehl schwer zu zerkleinern, was die Effizienz beeinträchtigt.
2. Lösung: Der Einsatz von Rapskuchen wurde erhöht und hochwertige lokale Zutaten wie Reiskleie wurden der Rezeptur hinzugefügt. Zusätzlich wurde Weizen hinzugefügt, der etwa 5–8 % der Rezeptur ausmacht. Durch die Anpassung ist der Granulationseffekt im Jahr 2009 relativ optimal, und auch der Ertrag pro Tonne konnte gesteigert werden. Die 2,5 mm großen Partikel liegen zwischen 8–9 Tonnen, was einer Steigerung von fast 2 Tonnen gegenüber dem Vorjahr entspricht. Auch das Aussehen der Partikel hat sich deutlich verbessert.
Um die Effizienz des Zerkleinerns von Baumwollsamenmehl zu verbessern, haben wir Baumwollsamenmehl und Rapsmehl vor dem Zerkleinern im Verhältnis 2:1 gemischt. Nach der Verbesserung war die Zerkleinerungsgeschwindigkeit im Wesentlichen mit der Zerkleinerungsgeschwindigkeit von Rapsmehl vergleichbar.
2. Unebene Oberfläche der Partikel
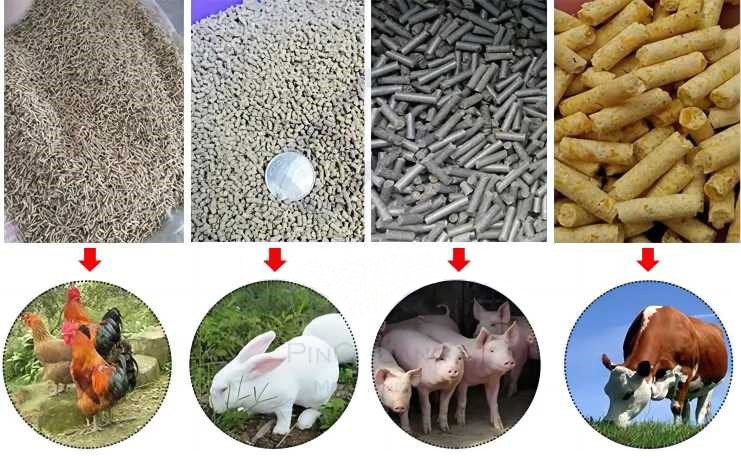
1. Es hat einen großen Einfluss auf das Aussehen des fertigen Produkts. Wenn es Wasser zugesetzt wird, neigt es zum Kollabieren und weist eine geringe Auslastungsrate auf. Der Hauptgrund ist:
(1) Die Rohstoffe werden zu grob zerkleinert und sind während des Temperierprozesses nicht vollständig ausgereift und erweicht und können beim Passieren der Formlöcher nicht gut mit anderen Rohstoffen kombiniert werden.
(2) Bei Fischfutterformeln mit hohem Rohfasergehalt entstehen während des Temperiervorgangs Dampfblasen im Rohmaterial. Diese Blasen platzen aufgrund des Druckunterschieds zwischen der Innen- und Außenseite der Form während der Partikelkompression, was zu einer unebenen Oberfläche der Partikel führt.
2. Handhabungsmaßnahmen:
(1) Kontrollieren Sie den Zerkleinerungsprozess richtig
Derzeit verwendet unser Unternehmen bei der Herstellung von Fischfutter 1,2 mm Sieb-Mikropulver als Hauptrohstoff. Wir kontrollieren die Häufigkeit der Siebnutzung und den Verschleißgrad des Hammers, um die Feinheit des Zerkleinerns sicherzustellen.
(2) Dampfdruck regeln
Passen Sie den Dampfdruck während der Produktion entsprechend der Formel angemessen an und halten Sie ihn im Allgemeinen bei etwa 0,2. Aufgrund der großen Menge an grobfaserigen Rohstoffen in der Fischfutterformel sind hochwertiger Dampf und eine angemessene Temperierzeit erforderlich.
3. Schlechte Wasserbeständigkeit der Partikel
1. Diese Art von Problem kommt in unserer täglichen Produktion am häufigsten vor und hängt im Allgemeinen mit den folgenden Faktoren zusammen:
(1) Kurze Temperierzeit und niedrige Temperiertemperatur führen zu ungleichmäßiger oder unzureichender Temperierung, niedrigem Reifegrad und unzureichender Feuchtigkeit.
(2) Unzureichende Klebematerialien wie Stärke.
(3) Das Kompressionsverhältnis der Ringform ist zu niedrig.
(4) Der Ölgehalt und der Anteil an Rohfaserrohstoffen in der Rezeptur sind zu hoch.
(5) Zerkleinerungspartikelgrößenfaktor.
2. Handhabungsmaßnahmen:
(1) Verbessern Sie die Dampfqualität, passen Sie den Flügelwinkel des Reglers an, verlängern Sie die Temperierzeit und erhöhen Sie den Feuchtigkeitsgehalt der Rohstoffe entsprechend.
(2) Passen Sie die Formel an, erhöhen Sie die Stärkerohstoffe entsprechend und reduzieren Sie den Anteil an Fett- und Rohfaserrohstoffen.
(3) Bei Bedarf Klebstoff hinzufügen. (Natriumbasierte Bentonit-Aufschlämmung)
(4) Verbessern Sie das Kompressionsverhältnis derRingmatrize
(5) Kontrollieren Sie die Feinheit des Zerkleinerns gut
4. Zu hoher Pulveranteil in den Partikeln
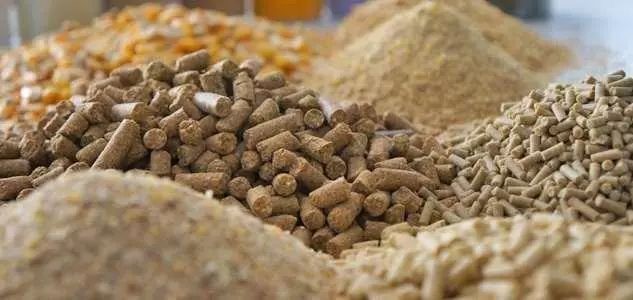
1. Es ist schwierig, das Aussehen des allgemeinen Pelletfutters nach dem Abkühlen und vor dem Sieben sicherzustellen. Kunden haben berichtet, dass die Pellets mehr Feinasche und Pulver enthalten. Basierend auf der obigen Analyse denke ich, dass es dafür mehrere Gründe gibt:
A. Die Partikeloberfläche ist nicht glatt, der Einschnitt ist nicht sauber und die Partikel sind locker und neigen zur Pulverbildung.
B. Unvollständige Siebung durch das Sortiersieb, verstopftes Siebgewebe, starker Verschleiß der Gummibälle, nicht passende Siebgewebeöffnung usw.;
C. Im Lager für Fertigprodukte befinden sich viele feine Ascherückstände und die Räumung ist nicht gründlich.
D. Bei der Staubentfernung während des Verpackens und Wiegens gibt es versteckte Gefahren.
Handhabungsmaßnahmen:
A. Optimieren Sie die Formelstruktur, wählen Sie die Ringdüse sinnvoll aus und kontrollieren Sie das Kompressionsverhältnis gut.
B. Kontrollieren Sie während des Granulationsprozesses die Temperierzeit, die Zufuhrmenge und die Granulationstemperatur, um die Rohstoffe vollständig reifen und erweichen zu lassen.
C. Achten Sie auf einen sauberen Partikelquerschnitt und verwenden Sie ein weiches Schneidmesser aus Bandstahl.
D. Passen Sie den Bewertungsbildschirm an und pflegen Sie ihn, und verwenden Sie eine sinnvolle Bildschirmkonfiguration.
E. Der Einsatz einer Sekundärsiebtechnologie im Fertigproduktlager kann den Pulvergehalt erheblich reduzieren.
F. Das Fertigproduktlager und der Kreislauf müssen rechtzeitig gereinigt werden. Darüber hinaus ist es notwendig, die Verpackungs- und Entstaubungsvorrichtung zu verbessern. Am besten ist es, Unterdruck zur Staubentfernung zu verwenden, was idealer ist. Insbesondere während des Verpackungsprozesses sollte der Verpackungsmitarbeiter den Pufferbehälter der Verpackungswaage regelmäßig abklopfen und den Staub entfernen..
5. Partikellänge variiert
1. In der täglichen Produktion stoßen wir häufig auf Schwierigkeiten bei der Steuerung, insbesondere bei Modellen über 420. Die Gründe hierfür lassen sich grob wie folgt zusammenfassen:
(1) Die Zufuhrmenge für die Granulierung ist ungleichmäßig und der Temperierungseffekt schwankt stark.
(2) Ungleichmäßiger Abstand zwischen den Formrollen oder starker Verschleiß der Ringform und der Druckrollen.
(3) Entlang der axialen Richtung der Ringform ist die Ausstoßgeschwindigkeit an beiden Enden geringer als in der Mitte.
(4) Das Druckreduzierloch der Ringform ist zu groß und die Öffnungsrate zu hoch.
(5) Die Position und der Winkel der Schneidklinge sind unangemessen.
(6) Granulationstemperatur.
(7) Die Art und die effektive Höhe (Klingenbreite, Breite) der Ringstanzklinge haben einen Einfluss.
(8) Gleichzeitig ist die Verteilung der Rohstoffe in der Kompressionskammer ungleichmäßig.
2. Die Qualität von Futtermitteln und Pellets wird im Allgemeinen anhand ihrer inneren und äußeren Eigenschaften analysiert. Als Produktionssystem sind wir stärker mit der äußeren Qualität von Futterpellets konfrontiert. Aus Produktionssicht lassen sich die Faktoren, die die Qualität von Futterpellets für Aquarien beeinflussen, grob wie folgt zusammenfassen:
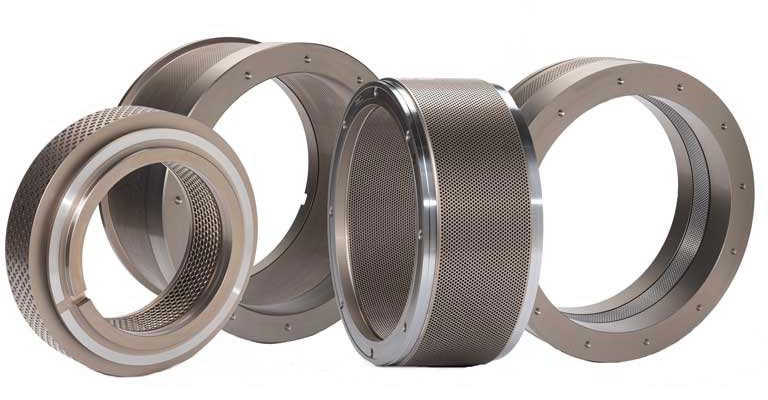
(1) Die Gestaltung und Organisation der Rezepturen hat einen direkten Einfluss auf die Qualität der Futterpellets für Wassertiere und macht etwa 40 % der Gesamtmenge aus.
(2) Die Intensität des Zerkleinerns und die Gleichmäßigkeit der Partikelgröße;
(3) Durchmesser, Kompressionsverhältnis und Lineargeschwindigkeit der Ringform wirken sich auf Länge und Durchmesser der Partikel aus.
(4) Das Kompressionsverhältnis, die lineare Geschwindigkeit, der Abschreck- und Anlasseffekt der Ringform und der Einfluss der Schneidklinge auf die Länge der Partikel;
(5) Der Feuchtigkeitsgehalt der Rohstoffe, der Temperiereffekt, das Kühlen und Trocknen wirken sich auf den Feuchtigkeitsgehalt und das Aussehen der fertigen Produkte aus.
(6) Die Ausrüstung selbst, Prozessfaktoren sowie Abschreck- und Anlasseffekte wirken sich auf den Partikelpulvergehalt aus.
3. Handhabungsmaßnahmen:
(1) Passen Sie Länge, Breite und Winkel des Stoffschabers an und ersetzen Sie den abgenutzten Schaber.
(2) Achten Sie darauf, die Position der Schneidklinge zu Beginn und gegen Ende der Produktion aufgrund der geringen Vorschubmenge rechtzeitig anzupassen.
(3) Stellen Sie während des Produktionsprozesses eine stabile Zufuhrrate und Dampfversorgung sicher. Wenn der Dampfdruck niedrig ist und die Temperatur nicht steigen kann, sollte er rechtzeitig angepasst oder gestoppt werden.
(4) Passen Sie den Abstand zwischen denWalzenmantel. Folgen Sie der neuen Form mit neuen Rollen und reparieren Sie umgehend die unebene Oberfläche der Druckrolle und der Ringform aufgrund von Verschleiß.
(5) Reparieren Sie das Führungsloch der Ringform und reinigen Sie das verstopfte Formloch umgehend.
(6) Bei der Bestellung der Ringform kann das Kompressionsverhältnis der drei Lochreihen an beiden Enden der axialen Richtung der ursprünglichen Ringform 1-2 mm kleiner sein als das in der Mitte.
(7) Verwenden Sie ein weiches Schneidemesser mit einer Dicke zwischen 0,5 und 1 mm, um eine möglichst scharfe Kante zu gewährleisten, sodass es sich auf der Eingriffslinie zwischen der Ringform und der Druckrolle befindet.
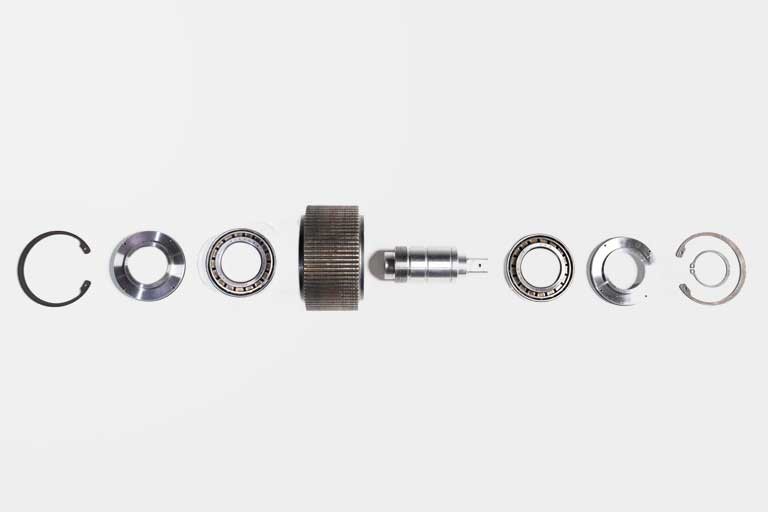
(8) Stellen Sie die Konzentrizität der Ringform sicher, überprüfen Sie regelmäßig das Spindelspiel des Granulators und passen Sie es gegebenenfalls an.
6. Zusammenfassung der Kontrollpunkte:
1. Mahlen: Die Mahlfeinheit muss entsprechend den Spezifikationsanforderungen kontrolliert werden
2. Mischen: Die Gleichmäßigkeit der Rohstoffmischung muss kontrolliert werden, um eine angemessene Mischmenge, Mischzeit, Feuchtigkeitsgehalt und Temperatur sicherzustellen.
3. Reifung: Druck, Temperatur und Feuchtigkeit der Puffmaschine müssen kontrolliert werden
Größe und Form des Partikelmaterials: Es müssen geeignete Spezifikationen für Pressformen und Schneidklingen ausgewählt werden.
5. Wassergehalt des fertigen Futters: Es ist notwendig, die Trocknungs- und Kühlzeit und -temperatur sicherzustellen.
6. Ölsprühen: Es ist notwendig, die genaue Menge des gesprühten Öls, die Anzahl der Düsen und die Qualität des Öls zu kontrollieren.
7. Siebung: Wählen Sie die Siebgröße entsprechend den Materialspezifikationen.
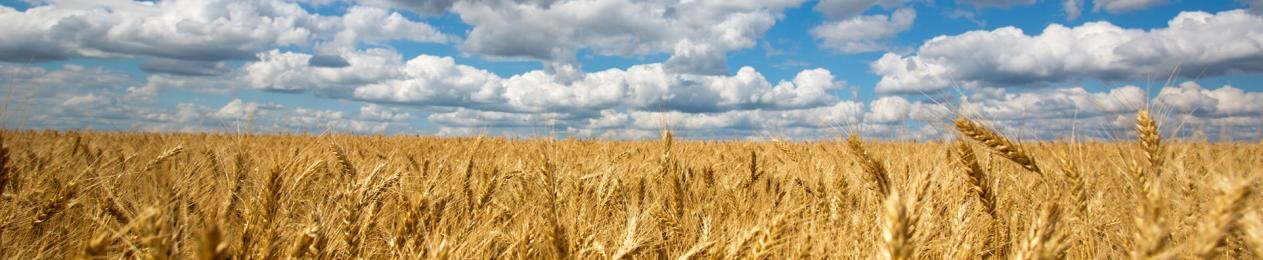
Veröffentlichungszeit: 30. November 2023