Schlechte Wasserbeständigkeit, unebene Oberfläche, hoher Pulvergehalt und ungleichmäßige Länge?Häufige Probleme und Verbesserungsmaßnahmen bei der Wasserfutterproduktion
Bei unserer täglichen Produktion von Wasserfutter sind wir in verschiedener Hinsicht auf einige Probleme gestoßen.Hier sind einige Beispiele, die Sie mit allen besprechen können:
1、 Formel
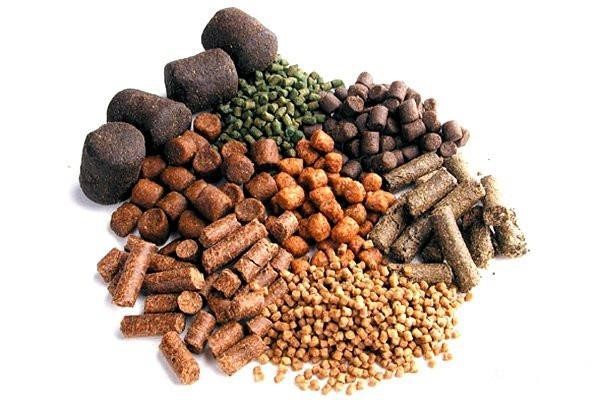
1. In der Formelstruktur von Fischfutter gibt es weitere Arten von Mehlrohstoffen, wie Rapsmehl, Baumwollmehl usw., die zu den Rohfasern gehören.Einige Ölfabriken verfügen über fortschrittliche Technologie und das Öl wird grundsätzlich trocken mit sehr geringem Inhalt frittiert.Darüber hinaus werden diese Arten von Rohstoffen bei der Produktion nicht leicht absorbiert, was große Auswirkungen auf die Granulierung hat.Darüber hinaus ist Baumwollmehl schwer zu zerkleinern, was die Effizienz beeinträchtigt.
2. Lösung: Die Verwendung von Rapskuchen wurde erhöht und die Rezeptur um hochwertige lokale Zutaten wie Reiskleie erweitert.Zusätzlich wurde Weizen hinzugefügt, der etwa 5–8 % der Formel ausmacht.Durch die Anpassung ist der Granulationseffekt im Jahr 2009 relativ ideal und auch der Ertrag pro Tonne ist gestiegen.Die 2,5-mm-Partikel wiegen zwischen 8 und 9 Tonnen, was einer Steigerung von fast 2 Tonnen im Vergleich zur Vergangenheit entspricht.Auch das Aussehen der Partikel hat sich deutlich verbessert.
Um die Effizienz beim Zerkleinern von Baumwollsamenmehl zu verbessern, haben wir außerdem vor dem Zerkleinern Baumwollsamenmehl und Rapsmehl im Verhältnis 2:1 gemischt.Nach der Verbesserung lag die Zerkleinerungsgeschwindigkeit im Wesentlichen auf dem Niveau der Zerkleinerungsgeschwindigkeit von Rapsschrot.
2、 Unebene Oberfläche der Partikel
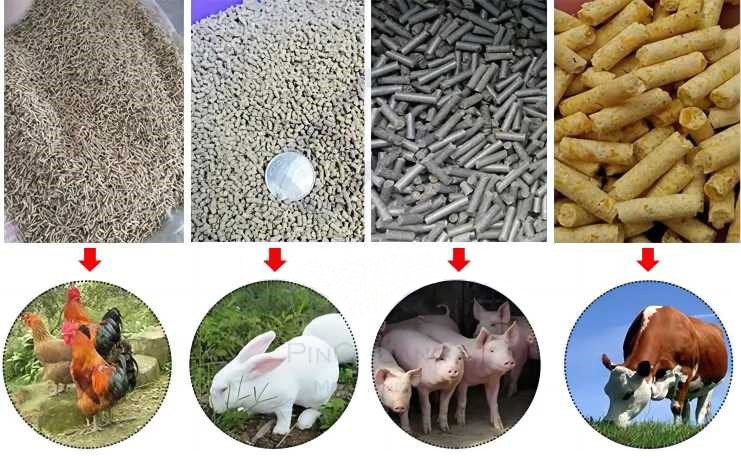
1. Es hat einen großen Einfluss auf das Aussehen des Endprodukts und neigt bei Zugabe zu Wasser zum Zusammenbruch und weist eine geringe Ausnutzungsrate auf.Der Hauptgrund ist:
(1) Die Rohstoffe werden zu grob zerkleinert, während des Temperiervorgangs werden sie nicht vollständig ausgereift und erweicht und können beim Durchgang durch die Formlöcher nicht gut mit anderen Rohstoffen kombiniert werden.
(2) In der Fischfutterformel mit einem hohen Rohfasergehalt platzen diese Blasen aufgrund des Vorhandenseins von Dampfblasen im Rohmaterial während des Temperiervorgangs aufgrund des Druckunterschieds zwischen innerhalb und außerhalb der Form während der Partikelkomprimierung. Dies führt zu einer unebenen Oberfläche der Partikel.
2. Handhabungsmaßnahmen:
(1) Kontrollieren Sie den Zerkleinerungsprozess ordnungsgemäß
Derzeit verwendet unser Unternehmen bei der Herstellung von Fischfutter 1,2-mm-Siebmikropulver als Hauptrohstoff.Wir kontrollieren die Einsatzhäufigkeit des Siebes und den Grad der Abnutzung des Hammers, um die Feinheit der Zerkleinerung sicherzustellen.
(2) Dampfdruck kontrollieren
Passen Sie den Dampfdruck gemäß der Formel während der Produktion angemessen an und kontrollieren Sie ihn im Allgemeinen auf etwa 0,2.Aufgrund des großen Anteils grobfaseriger Rohstoffe in der Fischfutterformel sind hochwertiger Dampf und eine angemessene Temperierungszeit erforderlich.
3, Schlechte Wasserbeständigkeit der Partikel
1. Diese Art von Problem kommt in unserer täglichen Produktion am häufigsten vor und hängt im Allgemeinen mit den folgenden Faktoren zusammen:
(1) Kurze Temperzeiten und niedrige Tempertemperaturen führen zu ungleichmäßiger oder unzureichender Temperierung, niedrigem Reifegrad und unzureichender Feuchtigkeit.
(2) Unzureichende Klebematerialien wie Stärke.
(3) Das Kompressionsverhältnis der Ringform ist zu niedrig.
(4) Der Ölgehalt und der Anteil an Rohfaserrohstoffen in der Rezeptur sind zu hoch.
(5) Zerkleinerungspartikelgrößenfaktor.
2. Handhabungsmaßnahmen:
(1) Verbessern Sie die Dampfqualität, stellen Sie den Flügelwinkel des Reglers ein, verlängern Sie die Temperierzeit und erhöhen Sie den Feuchtigkeitsgehalt der Rohstoffe entsprechend.
(2) Passen Sie die Formel an, erhöhen Sie die Stärkerohstoffe entsprechend und reduzieren Sie den Anteil an Fett- und Rohfaserrohstoffen.
(3) Fügen Sie bei Bedarf Klebstoff hinzu.(Natriumbasierte Bentonit-Aufschlämmung)
(4) Verbessern Sie das Komprimierungsverhältnis desRing sterben
(5) Kontrollieren Sie die Feinheit der Zerkleinerung gut
4、 Zu hoher Pulveranteil in Partikeln
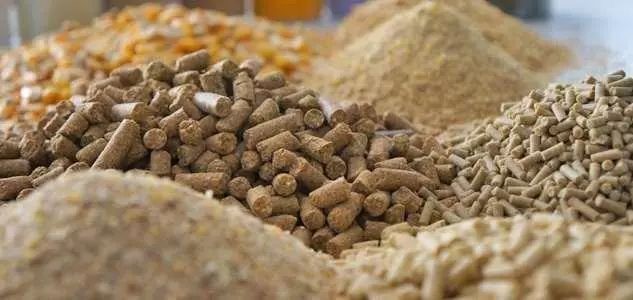
1. Es ist schwierig, das Aussehen des allgemeinen Pelletfutters nach dem Abkühlen und vor dem Sieben sicherzustellen.Kunden haben berichtet, dass die Pellets mehr feine Asche und Pulver enthalten.Basierend auf der obigen Analyse denke ich, dass es dafür mehrere Gründe gibt:
A. Die Partikeloberfläche ist nicht glatt, der Einschnitt ist nicht sauber und die Partikel sind locker und neigen zur Pulverproduktion;
B. Unvollständige Siebung durch Siebsieb, verstopfte Siebmaschen, starker Verschleiß der Gummibälle, nicht übereinstimmende Siebmaschenöffnungen usw.;
C. Im Fertigproduktlager befinden sich viele feine Ascherückstände und die Räumung ist nicht gründlich.
D. Die Staubentfernung beim Verpacken und Wiegen birgt versteckte Gefahren.
Handhabungsmaßnahmen:
A. Optimieren Sie die Formelstruktur, wählen Sie die Ringmatrize sinnvoll aus und kontrollieren Sie das Kompressionsverhältnis gut.
B. Kontrollieren Sie während des Granulierungsprozesses die Temperierzeit, die Zufuhrmenge und die Granulierungstemperatur, um die Rohstoffe vollständig zu reifen und weich zu machen.
C. Stellen Sie sicher, dass der Partikelquerschnitt sauber ist, und verwenden Sie ein weiches Schneidmesser aus Stahlband.
D. Passen Sie den Bewertungsbildschirm an, warten Sie ihn und verwenden Sie eine angemessene Bildschirmkonfiguration.
E. Der Einsatz sekundärer Siebtechnologie im Fertigproduktlager kann das Pulvergehaltsverhältnis erheblich reduzieren.
F. Es ist notwendig, das Lager und den Kreislauf der fertigen Produkte rechtzeitig zu reinigen.Darüber hinaus ist es notwendig, die Verpackungs- und Staubentfernungsvorrichtung zu verbessern.Für die Staubentfernung ist es am besten, Unterdruck zu verwenden, was idealer ist.Insbesondere während des Verpackungsprozesses sollte der Verpackungsarbeiter regelmäßig den Puffertrichter der Verpackungswaage ausklopfen und von Staub befreien.
5、 Die Partikellänge variiert
1. In der täglichen Produktion stoßen wir häufig auf Schwierigkeiten bei der Steuerung, insbesondere bei Modellen über 420. Die Gründe hierfür lassen sich grob wie folgt zusammenfassen:
(1) Die Zufuhrmenge für die Granulierung ist ungleichmäßig und der Temperierungseffekt schwankt stark.
(2) Ungleichmäßiger Spalt zwischen den Formrollen oder starker Verschleiß der Ringform und der Druckrollen.
(3) Entlang der Axialrichtung der Ringform ist die Austragsgeschwindigkeit an beiden Enden geringer als in der Mitte.
(4) Das Druckreduzierungsloch der Ringform ist zu groß und die Öffnungsrate ist zu hoch.
(5) Die Position und der Winkel des Schneidmessers sind unangemessen.
(6) Granulierungstemperatur.
(7) Die Art und die effektive Höhe (Klingenbreite, Breite) des Ringstanzmessers haben einen Einfluss.
(8) Gleichzeitig ist die Verteilung der Rohstoffe innerhalb der Kompressionskammer ungleichmäßig.
2. Die Qualität von Futtermitteln und Pellets wird im Allgemeinen anhand ihrer inneren und äußeren Eigenschaften analysiert.Als Produktionssystem sind wir stärker den Faktoren ausgesetzt, die mit der äußeren Qualität von Futterpellets zusammenhängen.Aus produktionstechnischer Sicht lassen sich die Faktoren, die die Qualität von Wasserfutterpellets beeinflussen, grob wie folgt zusammenfassen:
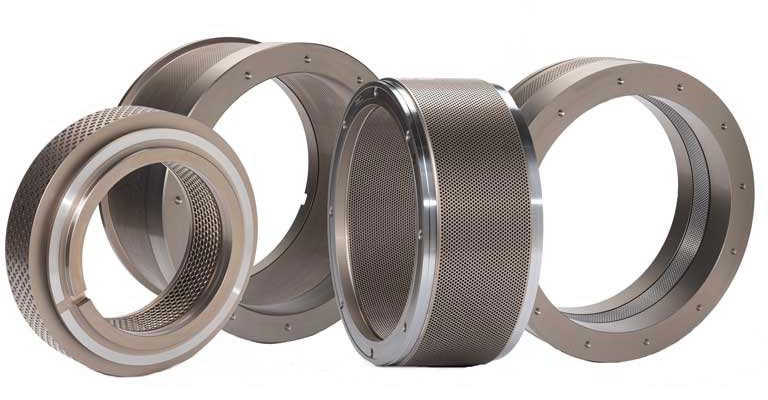
(1) Die Gestaltung und Organisation der Rezepturen hat einen direkten Einfluss auf die Qualität der Wasserfutterpellets und macht etwa 40 % der Gesamtmenge aus;
(2) Die Intensität der Zerkleinerung und die Gleichmäßigkeit der Partikelgröße;
(3) Der Durchmesser, das Kompressionsverhältnis und die lineare Geschwindigkeit der Ringform haben einen Einfluss auf die Länge und den Durchmesser der Partikel;
(4) Das Kompressionsverhältnis, die lineare Geschwindigkeit, der Abschreck- und Tempereffekt der Ringform und der Einfluss des Schneidmessers auf die Länge der Partikel;
(5) Der Feuchtigkeitsgehalt der Rohstoffe, der Temperiereffekt, die Kühlung und die Trocknung wirken sich auf den Feuchtigkeitsgehalt und das Aussehen der Endprodukte aus;
(6) Die Ausrüstung selbst, Prozessfaktoren sowie Abschreck- und Tempereffekte haben einen Einfluss auf den Partikelpulvergehalt;
3. Handhabungsmaßnahmen:
(1) Passen Sie Länge, Breite und Winkel des Stoffschabers an und ersetzen Sie den abgenutzten Schaber.
(2) Achten Sie darauf, die Position des Schneidmessers aufgrund der geringen Vorschubmenge rechtzeitig zu Beginn und gegen Ende der Produktion anzupassen.
(3) Sorgen Sie während des Produktionsprozesses für eine stabile Zufuhrrate und Dampfversorgung.Wenn der Dampfdruck niedrig ist und die Temperatur nicht ansteigen kann, sollte sie rechtzeitig angepasst oder gestoppt werden.
(4) Passen Sie den Abstand zwischen den angemessen anRollenmantel.Folgen Sie der neuen Form mit neuen Rollen und reparieren Sie umgehend die unebene Oberfläche der Druckrolle und der Ringform aufgrund von Verschleiß.
(5) Reparieren Sie das Führungsloch der Ringform und reinigen Sie umgehend das verstopfte Formloch.
(6) Bei der Bestellung der Ringform kann das Kompressionsverhältnis der drei Lochreihen an beiden Enden der axialen Richtung der ursprünglichen Ringform 1–2 mm kleiner sein als das in der Mitte.
(7) Verwenden Sie ein weiches Schneidmesser mit einer kontrollierten Dicke zwischen 0,5 und 1 mm, um eine möglichst scharfe Kante zu gewährleisten, sodass sie sich auf der Eingriffslinie zwischen der Ringform und der Andruckrolle befindet.
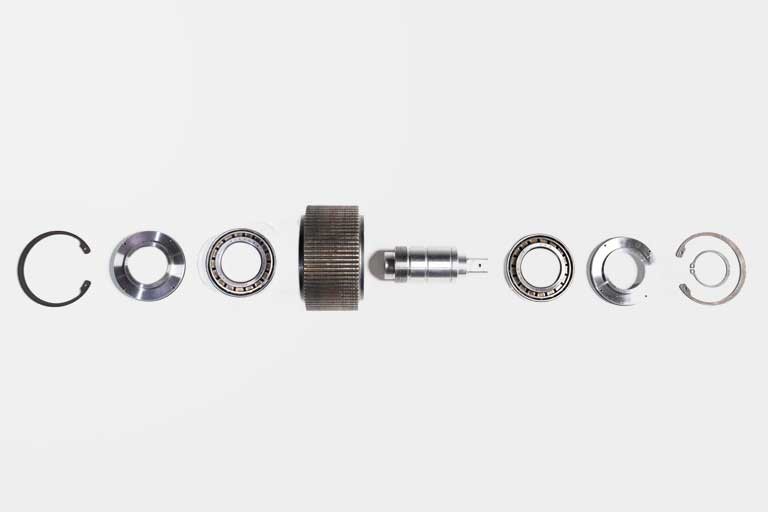
(8) Stellen Sie die Konzentrizität der Ringform sicher, überprüfen Sie regelmäßig den Spindelabstand des Granulators und stellen Sie ihn gegebenenfalls ein.
6、 Zusammenfassung Kontrollpunkte:
1. Mahlen: Die Mahlfeinheit muss gemäß den Spezifikationsanforderungen kontrolliert werden
2. Mischen: Die Gleichmäßigkeit der Rohstoffmischung muss kontrolliert werden, um eine angemessene Mischmenge, Mischzeit, Feuchtigkeitsgehalt und Temperatur sicherzustellen.
3. Reifung: Druck, Temperatur und Feuchtigkeit der Puffmaschine müssen kontrolliert werden
Die Größe und Form des Partikelmaterials: Es müssen geeignete Spezifikationen für Pressformen und Schneidmesser ausgewählt werden.
5. Wassergehalt des Fertigfutters: Es ist notwendig, die Trocknungs- und Kühlzeit sowie die Temperatur sicherzustellen.
6. Ölsprühen: Es ist notwendig, die genaue Menge des Ölsprühens, die Anzahl der Düsen und die Qualität des Öls zu kontrollieren.
7. Siebung: Wählen Sie die Größe des Siebes entsprechend den Spezifikationen des Materials.
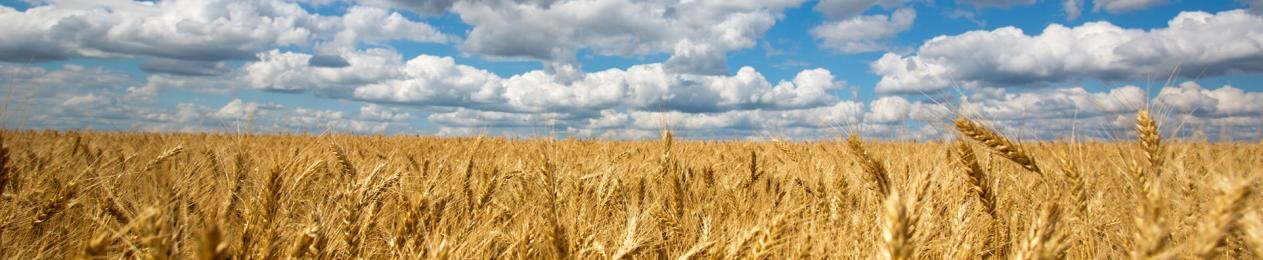
Zeitpunkt der Veröffentlichung: 30. November 2023