Unabhängig davon, ob es sich um eine Flachdüsen-Pelletmaschine oder eine Ringdüsen-Pelletmaschine handelt, besteht in der Granulierungsindustrie das Funktionsprinzip darin, sich auf die relative Bewegung zwischen dem Druckwalzengehäuse und der Form zu verlassen, um das Material zu ergreifen, in die effektive Station zu gelangen und es zu extrudieren Form und schneiden Sie es dann mit der Schneidklinge in Partikel der erforderlichen Länge.
Partikelpresswalzengehäuse
Das Druckwalzengehäuse besteht hauptsächlich aus einer Exzenterwelle, Wälzlagern, einem außerhalb der Druckwalzenwelle ummantelten Druckwalzengehäuse und Komponenten zur Unterstützung und Fixierung des Druckwalzengehäuses.
Der Druckwalzenmantel drückt das Material in das Formloch und formt es unter Druck im Formloch.Um ein Durchrutschen der Andruckrolle zu verhindern und die Greifkraft zu erhöhen, muss eine gewisse Reibungskraft zwischen Andruckrolle und Material vorhanden sein.Daher werden an der Oberfläche der Druckwalze häufig Maßnahmen zur Erhöhung der Reibung und der Verschleißfestigkeit ergriffen.Bei der Bestimmung der Strukturparameter der Druckwalze und der Form haben die Strukturform und die Größe der Außenfläche der Druckwalze einen erheblichen Einfluss auf die Granulationseffizienz und Partikelqualität.
Oberflächenstruktur des Druckwalzenmantels
Es gibt drei gängige Oberflächentypen für die vorhandenen Partikelpresswalzen: gerillte Walzenoberfläche, gerillte Walzenoberfläche mit Kantenversiegelung und Wabenwalzenoberfläche.
Die Druckwalze mit Zahnnut hat eine gute Rollleistung und wird häufig in Vieh- und Geflügelfutterfabriken eingesetzt.Aufgrund des Gleitens des Futters in der Zahnnut ist der Verschleiß der Druckwalze und der Ringform jedoch nicht sehr gleichmäßig und der Verschleiß an beiden Enden der Druckwalze und der Ringform ist stärker.
Die gezahnte Andrückwalze mit Kantenversiegelung ist vor allem für die Herstellung von Wassermaterialien geeignet.Aquatische Materialien neigen beim Extrudieren eher zum Verrutschen.Aufgrund der Kantenversiegelung auf beiden Seiten der Zahnnut ist es beim Futterauspressen nicht leicht, nach beiden Seiten zu rutschen, was zu einer gleichmäßigeren Futterverteilung führt.Auch der Verschleiß der Andruckrolle und der Ringform ist gleichmäßiger, was zu einer gleichmäßigeren Länge der produzierten Pellets führt.
Der Vorteil der Wabenwalze besteht darin, dass der Verschleiß der Ringform gleichmäßig ist und auch die Länge der produzierten Partikel relativ konstant ist.Allerdings ist die Leistung der Spule schlecht, was sich auf die Leistung des Granulators auswirkt und nicht so häufig vorkommt wie die Verwendung des Schlitztyps in der tatsächlichen Produktion.
Das Folgende ist eine Zusammenfassung von 10 Arten von Partikelmaschinen-Andruckrollen für Baoshell-Andruckrollen-Ringformen, und die letzten 3 sind definitiv diejenigen, die Sie noch nicht gesehen haben!
Nr. 10 Nuttyp
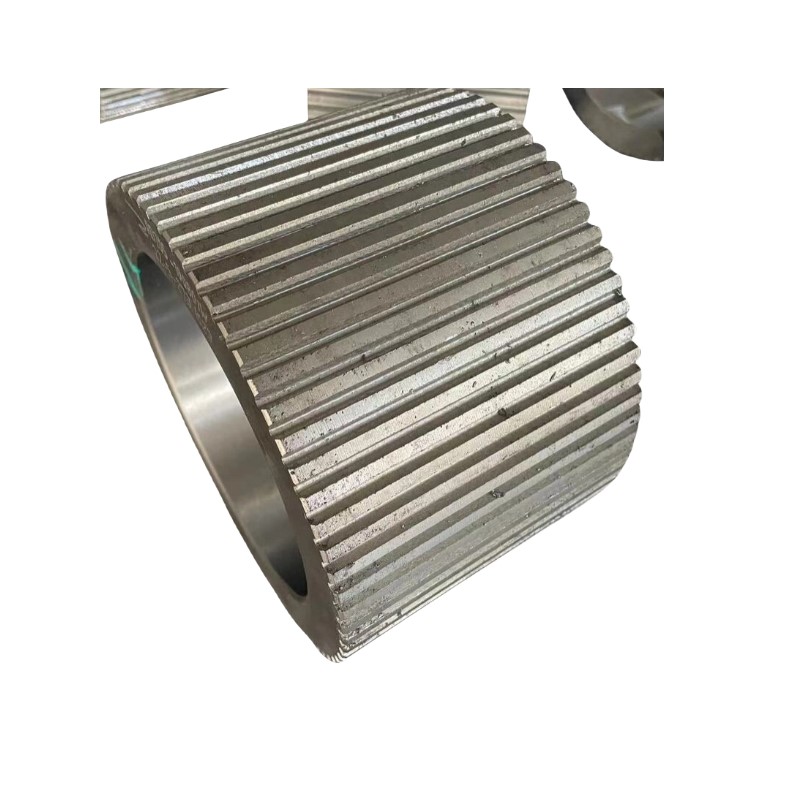
Nr. 9 Typ mit geschlossener Nut
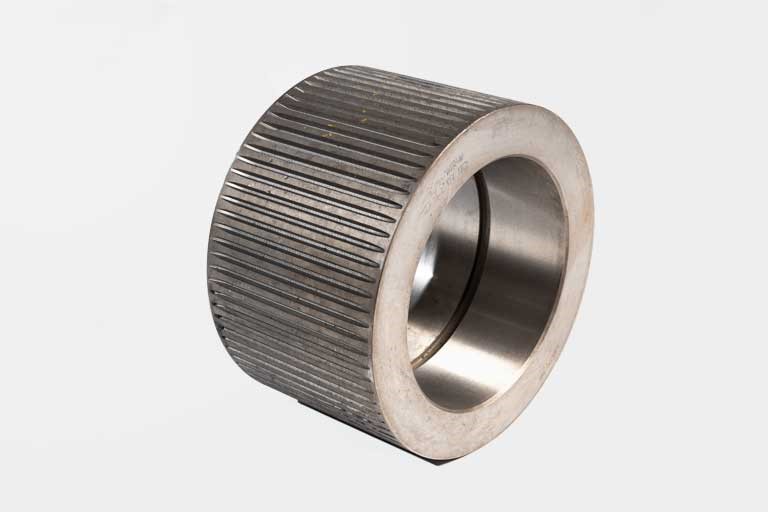
NO.8 Wabentyp
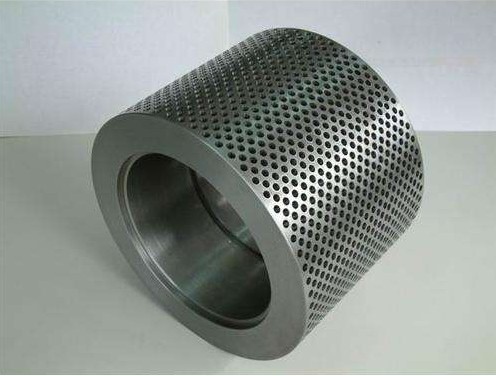
Nr. 7 Rautenförmig
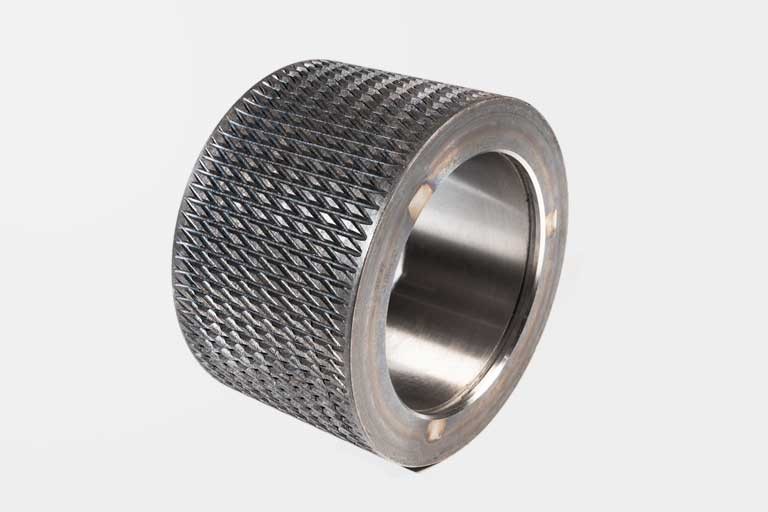
Nr. 6 Schrägrille
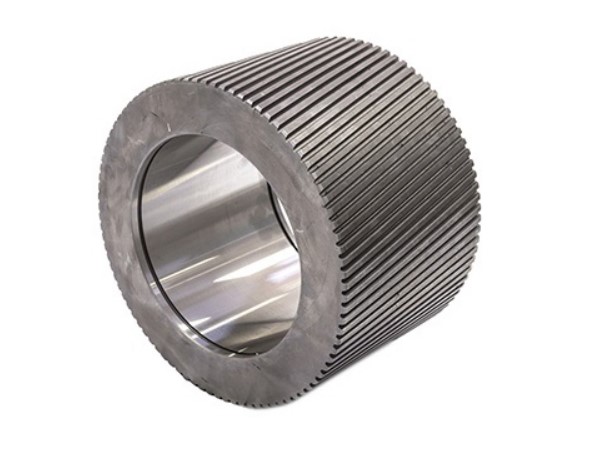
Nr. 5 Nut+Wabe
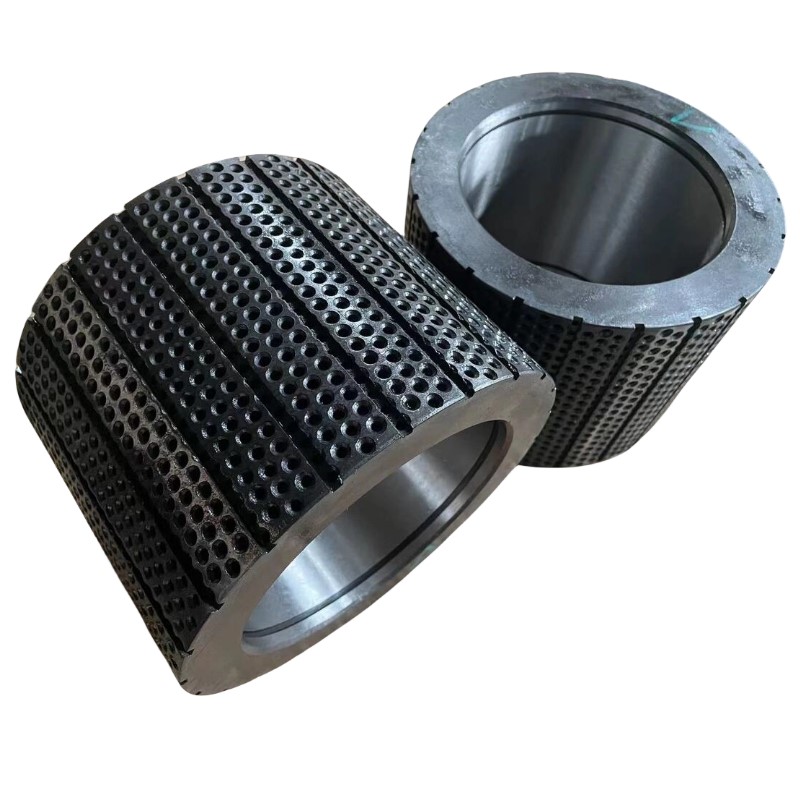
Nr. 4: Geschlossene Nut + Wabe
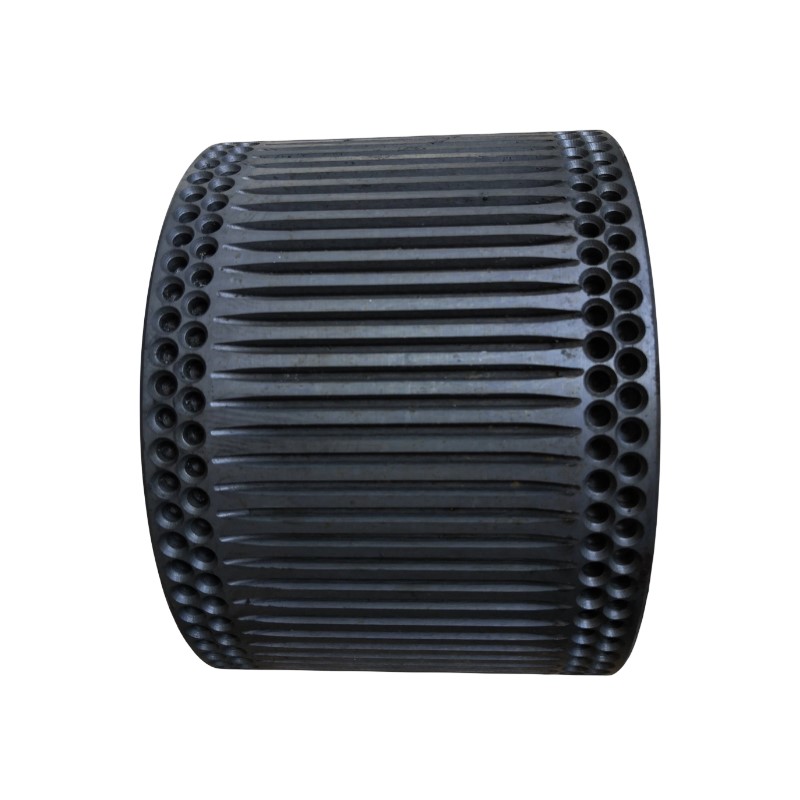
Nr. 3 Schrägrille + Wabe
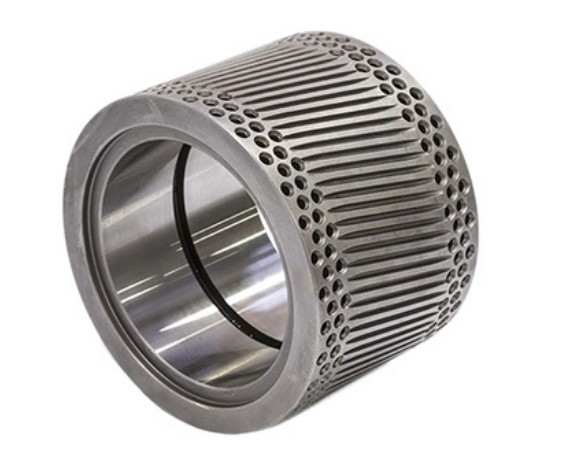
Nr. 2 Fischgrätenwelle
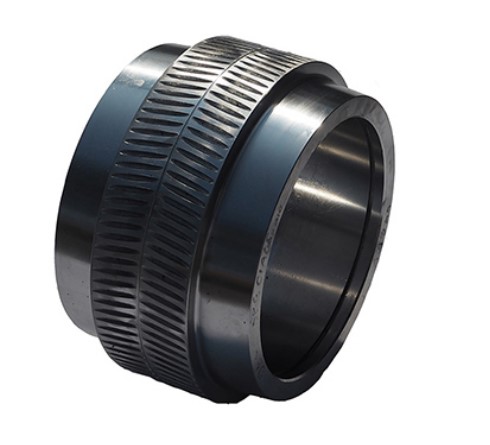
Nr. 1 Bogenförmige Welle
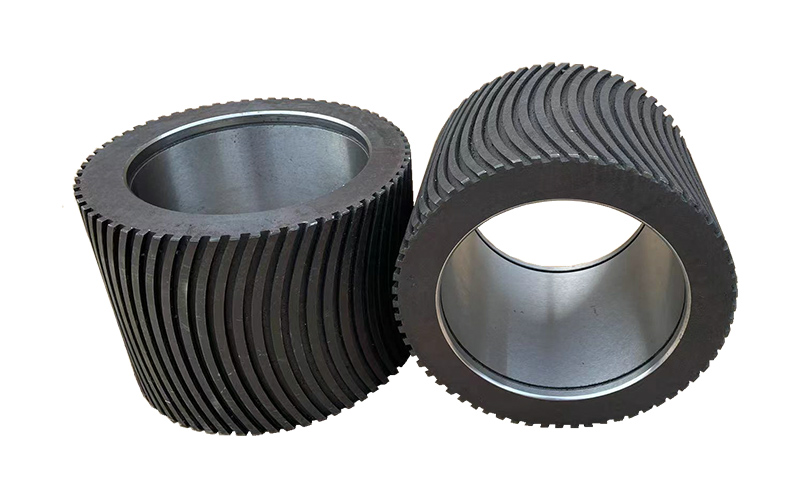
SONDERMODELL: KOLLERSCHALE AUS WOLFRAMCARBID
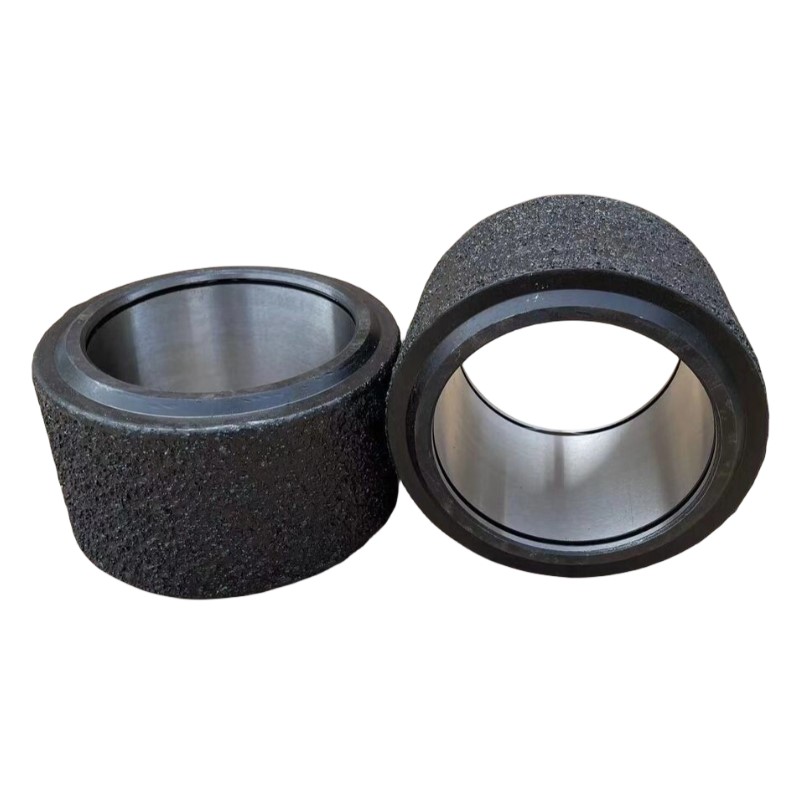
Die Behandlungsmethode für den Schlupf der Andruckwalze der Partikelmaschine
Aufgrund der rauen Arbeitsumgebung, der hohen Arbeitsintensität und der schnellen Verschleißrate des Druckwalzenmantels ist die Druckwalze ein anfälliger Teil der Partikelmaschine und muss regelmäßig ausgetauscht werden.In der Produktionspraxis hat sich gezeigt, dass, solange sich die Eigenschaften der Produktionsmaterialien ändern oder sich andere Bedingungen während der Verarbeitung ändern, das Phänomen des Durchrutschens der Andruckwalze der Partikelmaschine auftreten kann.Sollte es während des Granuliervorgangs zu einem Durchrutschen der Andruckwalze kommen, geraten Sie bitte nicht in Panik.Spezifische Details finden Sie in den folgenden Techniken:
Grund 1: Schlechte Rundlaufgenauigkeit der Andruckrollen- und Spindelmontage
Lösung:
Prüfen Sie, ob der Einbau der Druckrollenlager sinnvoll ist, um ein seitliches Ausweichen des Druckrollenmantels zu vermeiden.
Grund 2: Die Trichtermündung der Ringform ist flach geschliffen, wodurch die Form keine Materialien frisst
Lösung:
Überprüfen Sie den Verschleiß der Klemmen, Übertragungsräder und Auskleidungsringe des Granulators.
Passen Sie die Konzentrizität der Ringforminstallation mit einem Fehler von nicht mehr als 0,3 mm an.
Der Spalt zwischen den Andruckrollen sollte so eingestellt sein, dass die Hälfte der Arbeitsfläche der Andruckrollen mit der Form zusammenarbeitet und dass auch das Spalteinstellrad und die Feststellschraube in einwandfreiem Zustand sind.
Wenn die Andruckwalze durchrutscht, lassen Sie die Partikelmaschine nicht zu lange im Leerlauf und warten Sie, bis sie von selbst Material ausstößt.
Das Kompressionsverhältnis der verwendeten Ringformöffnung ist zu hoch, was zu einem hohen Materialaustrittswiderstand der Form führt und auch eine der Ursachen für das Durchrutschen der Andruckrolle ist.
Die Pelletmaschine sollte nicht unnötig im Leerlauf laufen, ohne dass Material zugeführt wird.
Grund 3: Das Druckrollenlager sitzt fest
Lösung:
Ersetzen Sie die Druckrollenlager.
Grund 4: Der Andruckrollenmantel ist nicht rund
Lösung:
Die Qualität des Walzenmantels ist einwandfrei. Ersetzen oder reparieren Sie den Walzenmantel.
Wenn die Andruckrolle durchrutscht, sollte sie rechtzeitig gestoppt werden, um eine längere Leerlaufreibung der Andruckrolle zu vermeiden.
Grund 5: Verbiegen oder Lockern der Andruckrollenspindel
Lösung:
Tauschen Sie die Spindel aus oder ziehen Sie sie fest und überprüfen Sie den Zustand der Andruckrollenspindel, wenn Sie die Ringform und die Andruckrolle austauschen.
Grund 6: Die Arbeitsfläche der Andruckrolle ist relativ falsch zur Arbeitsfläche der Ringform ausgerichtet (Kantenkreuzung)
Lösung:
Überprüfen Sie, ob die Andruckrolle nicht ordnungsgemäß installiert ist, und ersetzen Sie sie.
Prüfen Sie, ob die Exzenterwelle der Andruckrolle verformt ist.
Überprüfen Sie die Hauptwellenlager oder Buchsen der Partikelmaschine auf Verschleiß.
Grund 7: Der Spindelabstand des Granulators ist zu groß
Lösung:
Überprüfen Sie das Anzugsspiel des Granulators.
Grund 8: Die Stanzrate der Ringform ist niedrig (weniger als 98 %).
Lösung:
Bohren Sie mit einem Pistolenbohrer durch das Formloch oder kochen Sie es in Öl und mahlen Sie es vor dem Füttern.
Grund 9: Rohstoffe sind zu grob und haben einen hohen Feuchtigkeitsgehalt
Lösung:
Achten Sie auf einen Feuchtigkeitsgehalt von ca. 15 %.Wenn der Feuchtigkeitsgehalt der Rohstoffe zu hoch ist, kommt es nach dem Eintritt der Rohstoffe in die Ringform zu Verstopfungen und Verrutschen der Form.Der Feuchtigkeitskontrollbereich der Rohstoffe liegt zwischen 13 und 20 %.
Grund 10: Neue Form wird zu schnell zugeführt
Lösung:
Passen Sie die Geschwindigkeit an, um sicherzustellen, dass die Andruckrolle ausreichend Traktion hat, verhindern Sie ein Durchrutschen der Andruckrolle und prüfen Sie umgehend den Verschleiß der Ringform und der Andruckrolle.
Zeitpunkt der Veröffentlichung: 25. März 2024